Commercial and Automotive
powder coating

Powder coating is a popular method of applying a durable and attractive finish to a wide range of products and surfaces. It is commonly used in industries like automotive, manufacturing, construction, and more. Here’s an overview of powder coating:

What is Powder Coating?
Powder coating is a dry finishing process that involves the application of a fine, dry powder made of a mixture of finely ground particles of pigment and resin onto a surface. The powder is electrostatically charged, and the charged particles are sprayed onto the object to be coated. After the powder is applied, the coated object is heated in an oven, where the powder particles melt and fuse to create a solid, continuous, and durable coating.

Key Characteristics of Powder Coating:

- Durability: Powder coatings are known for their exceptional durability and resistance to various environmental factors, such as UV rays, moisture, chemicals, and corrosion. This makes them suitable for both indoor and outdoor applications.
- Versatility: Powder coating can be applied to a wide range of materials, including metal, plastics, glass, wood, and even MDF. It is used in industries like automotive, architectural, industrial, and consumer goods.
- Aesthetics: Powder coatings come in a vast array of colors and finishes, including glossy, matte, metallic, textured, and more. This allows for great design flexibility and the creation of visually appealing surfaces.
- Environmental Benefits: Powder coating is an environmentally friendly option compared to traditional liquid coatings, as it doesn’t contain solvents or emit harmful VOCs (volatile organic compounds). Overspray can also be recycled, reducing waste.


The Powder Coating Process:
- Surface Preparation: The item to be coated is cleaned and prepared to remove any contaminants like oils, rust, or old paint, ensuring proper adhesion of the powder. Sandblasting is the most effective form of preparation.
- Powder Application: The powder is applied using a spray gun, which gives the particles an electrostatic charge. This charge attracts the powder particles to the grounded object, creating an even and consistent layer.
- Curing: The coated object is placed in an oven where it is heated at a specified temperature for a set period. During this process, the powder particles melt and chemically react to create a solid and smooth coating.
- Cooling: After curing, the coated object is allowed to cool down, resulting in a hard and resilient finish.
Benefits of Powder Coating:
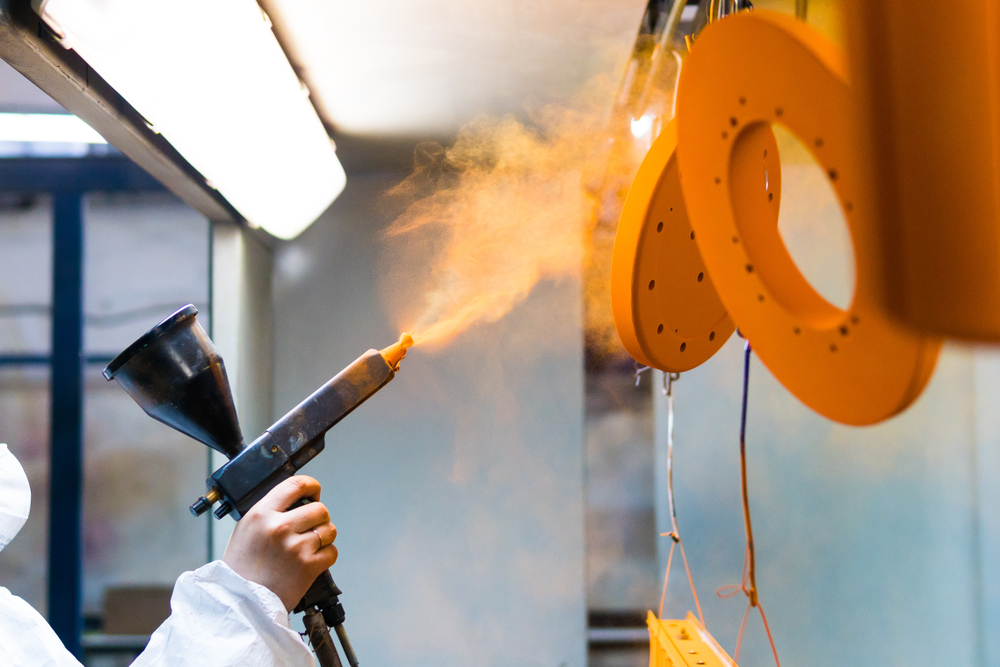
- Excellent durability and longevity
- Attractive and customizable finishes
- Resistance to corrosion and abrasion
- Reduced environmental impact
- Uniform and consistent coating
- Cost-effective due to minimal waste
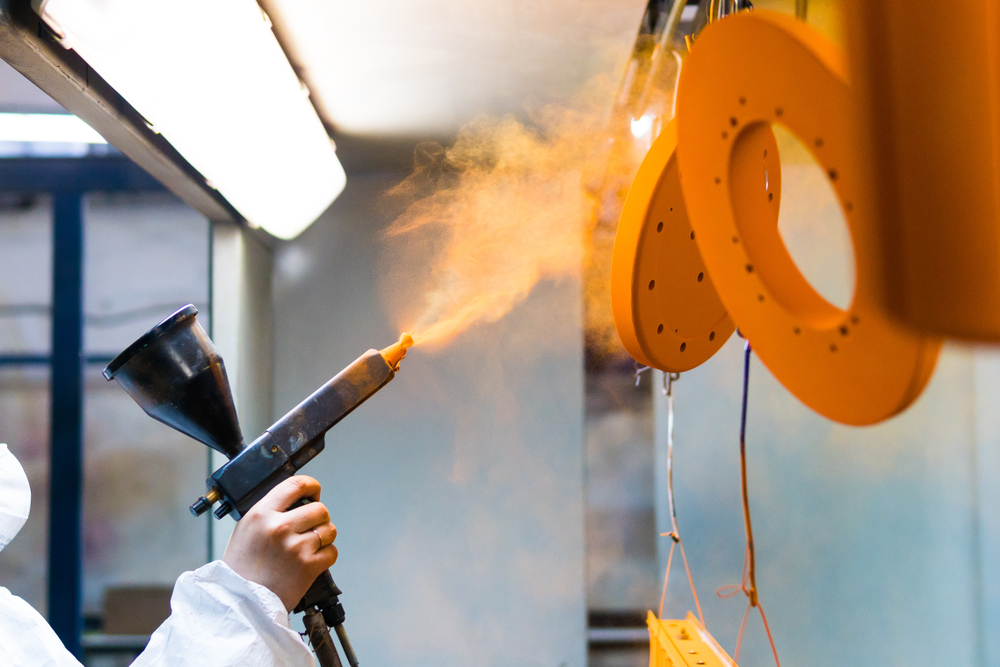

Applications of Powder Coating:
- Automotive parts (rims, frames, bumpers)
- Architectural elements (fences, railings, doors)
- Industrial machinery and equipment
- Household appliances
- Outdoor Furniture
- Outdoor equipment (patio furniture, playground equipment, gym equipment)
- Electronics
Brands of Powder used at Armadillo

- Tiger Drylac
- Prismatic Powders
- Columbia Coatings
- Vitracoat
- PPG
- Sherwin Williams
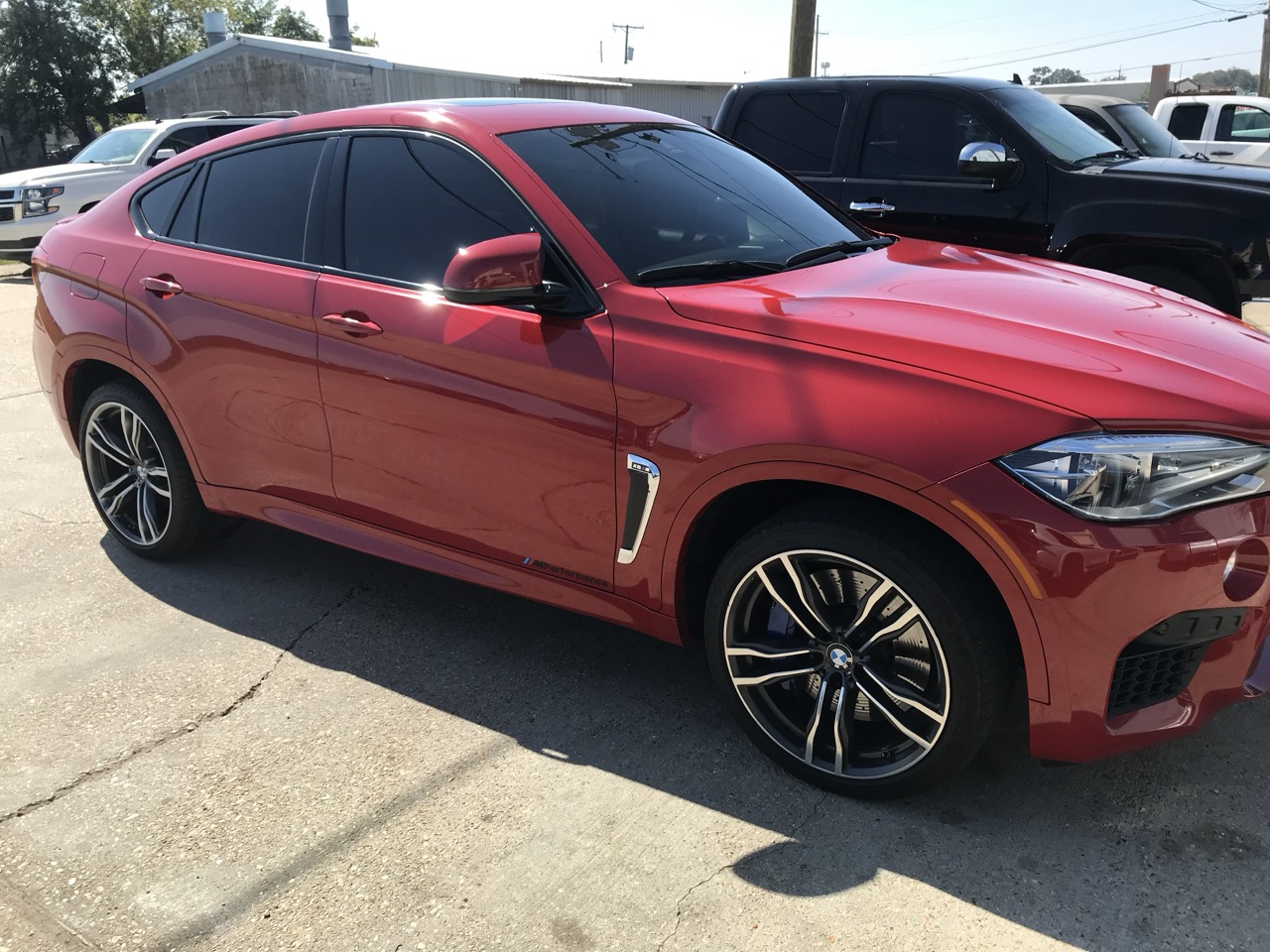
Powder coating has become increasingly popular as a superior alternative to traditional wet paint applications due to its durability, versatility, and environmental benefits. It provides a long-lasting and attractive finish for a wide range of products and surface.



